At its core, CNC milling includes the elimination of material from a workpiece with a series of collaborated activities. As soon as the layout is finished, the driver uses computer-aided production (CAM) software to equate the CAD design right into a collection of instructions that the CNC maker can read, generally in the kind of G-code.
One of the standout features of CNC milling is its convenience. Unlike conventional milling machines, which normally operate along one or 2 axes, CNC milling machines can operate on numerous axes at the same time-- commonly three, 4, or even five.
Explore cnc milling guide the transformative world of CNC milling, an innovation that combines accuracy and automation to generate top notch elements efficiently from various products, and find its processes, benefits, and vital factors to consider for success in contemporary manufacturing.
The option of devices is an additional important element of CNC milling. The suitable tool choice can considerably impact the top quality of the ended up product and the performance of the machining procedure.
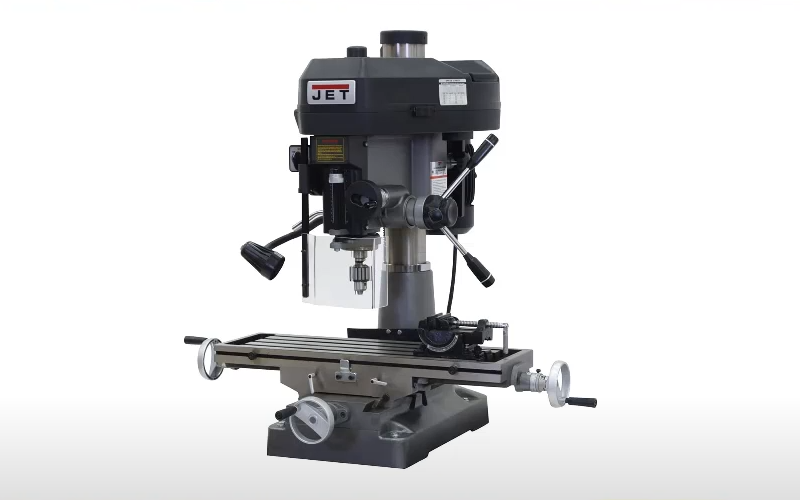
One vital factor to consider in CNC milling is material compatibility. Comprehending the properties of the material, including its firmness, machinability, and thermal conductivity, enables drivers to maximize the milling process and attain premium outcomes while lessening wear and tear on tools.
Beyond the technical factors like design, tooling, and materials, there are additional considerations for optimizing CNC milling procedures. Utilizing innovative attributes such as toolpath optimization strategies can enhance the milling procedure even more, enabling faster machining cycles and lowering waste.
In addition, among the considerable benefits of CNC milling is the capability to automate repetitive jobs, which lessens human error and enhances manufacturing uniformity. While traditional milling equipments require an experienced driver to manage the production procedure, CNC milling machines can run ignored, executing pre-programmed guidelines with precision. This level of automation not just improves effectiveness but also releases up experienced employees from mundane jobs, allowing them to concentrate on more valuable tasks such as quality assurance and procedure enhancement.
In spite of its advantages, transitioning to CNC milling is not without obstacles. The availability of leasing alternatives and inexpensive entry-level CNC milling makers has actually made it extra accessible for little and mid-sized businesses to adopt this technology.
Training and skill development for personnel operating CNC milling machines are also important for optimizing the return on financial investment. Operators need a strong understanding of both the CNC machine itself and the software program being used for shows and tracking. Numerous manufacturers locate success by supplying in-house training programs or partnering with exterior training organizations to outfit their teams with the essential skills and expertise.
In the last few years, technical advancements remain to form the field of CNC milling. As markets progressively transform to automation, integrating functions such as fabricated intelligence (AI) and device understanding right into CNC machines can even more improve the precision and effectiveness of milling procedures. Smart CNC systems, which integrate information and sensing units analytics, can check efficiency in real-time and make immediate modifications to enhance machining specifications or to identify wear and tear on devices. This data-driven technique holds the prospective to substantially minimize downtime and upkeep expenses while enhancing total efficiency.
Improvements in software program are continuously narrowing the space in between layout and production. Modern CAD/CAM systems currently provide much more user-friendly user interfaces and boosted simulation capacities, allowing operators to imagine machining processes before they are performed. By finding possible problems in the style phase, business can deal with design flaws or optimize reducing methods without incurring expensive alterations to physical products.
In the context of CNC milling, sustainability is likewise acquiring importance as suppliers try to find ways to lower their ecological impact. Applying methods such as optimizing reducing parameters, making use of much more reliable tooling, and recycling products can contribute to an extra sustainable milling procedure. Additionally, innovations such as additive production are being explored together with CNC milling, presenting chances for hybrid production strategies that better boost sustainability by lessening waste.
Check out benchtop milling machine the transformative world of CNC milling, a technology that incorporates accuracy and automation to produce high-grade elements efficiently from numerous materials, and uncover its processes, benefits, and key factors to consider for success in modern production.
Finally, CNC milling stands for an important property in modern manufacturing, offering companies with the ability to generate complicated and premium elements effectively. Its mix of precision, automation, and flexibility has made it a staple in industries ranging from aerospace to auto, clinical to consumer products. Understanding CNC milling starts with a solid structure in its processes, consisting of the interaction between layout, tooling, materials, and software. As modern technology remains to evolve, the possibility for competent drivers to take advantage of these improvements will just broaden, enabling greater performances and innovations in CNC milling applications. By remaining educated on best methods and emerging modern technologies, manufacturers can position themselves at the leading edge of this vibrant sector and fully exploit the abilities that CNC milling uses. Inevitably, effective assimilation of CNC milling equipment, skilled labor force training, and clever automation leads the means for the future of production, where quality, sustainability, and effectiveness become the trademarks of operational quality.